Glass has been used since ancient times as both a decorative and functional medium. Glass artists utilise a broad range of techniques to create magnificent colours, textures, shapes and patterns. Read on to discover the meaning of key terms techniques used in the art of glass:
Studio Glass
A term and movement popularised in the 1960s to describe limited edition or unique pieces made in a studio rather than a factory, often, but not necessarily, by one glass artist.
Trailing
The process of applying a thin softened thread of glass to the exterior of an object.
Zanfirico
Polychrome canes twisted together while simultaneously being drawn out between two pontils creating a spiral pattern. Also known as Vetro a Retorti.
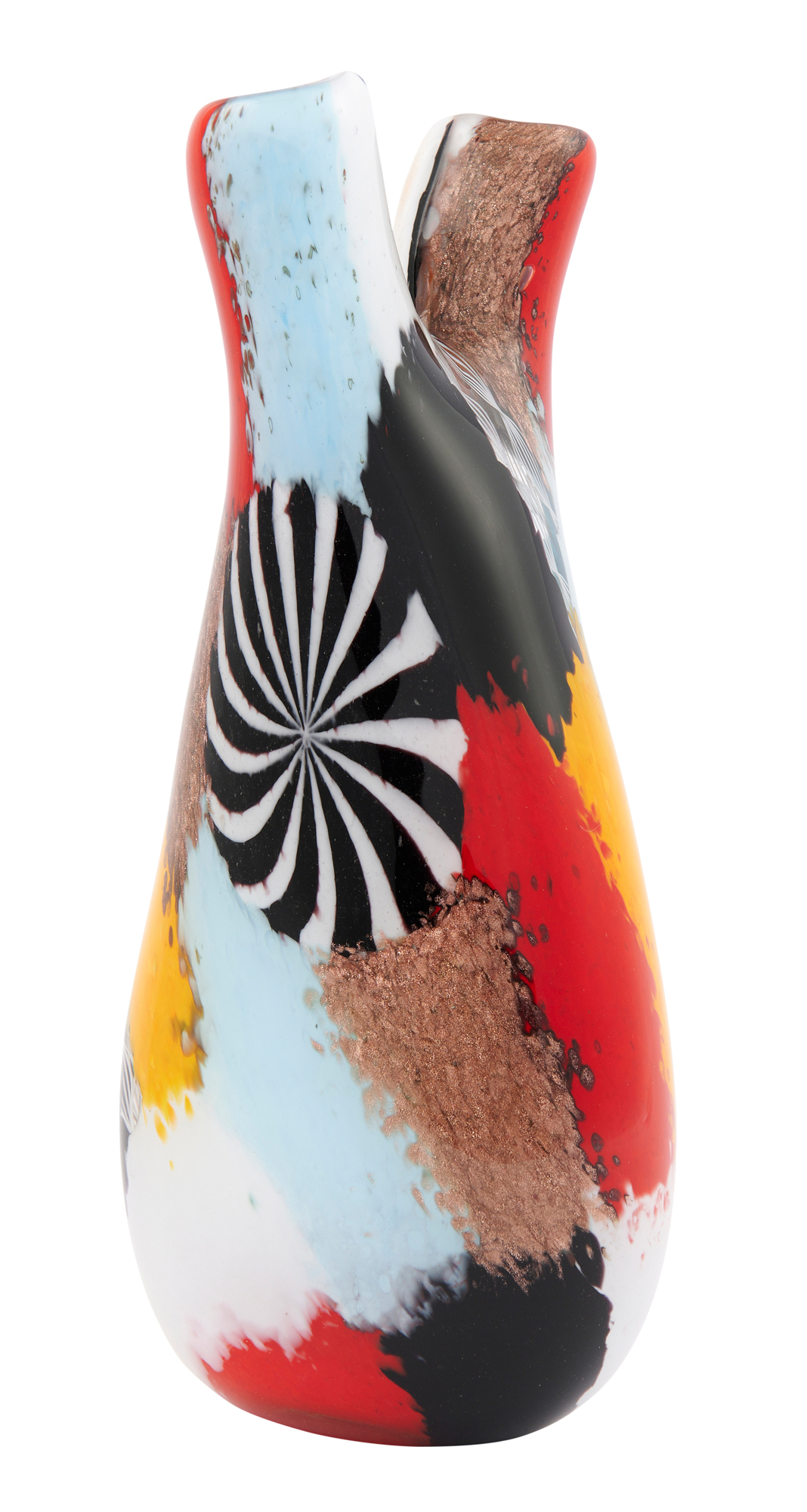
Vetro a Fili
‘Glass with threads’ used to describe blown glass with canes that form parallel lines
Reticello
Used to describe blown glass with a criss cross net like pattern of canes
Scavo
A surface application that when applied to a glass object and heated creates a similar effect to the look of ancient glass unearthed in an archeological excavation.
Aventurine
Translucent glass with sparkling inclusions of gold, copper, or chromic oxide. Imitating the mineral of the same name.
Battuto
Describes a multifaceted wheel-engraved surface that resembles beaten metal.
Annealing
The process of slowly cooling a completed object. If a hot glass object is allowed to cool too quickly, it will be highly strained by the time it reaches room temperature
Pontil
The pontil is a solid metal rod that is usually tipped with a wad of hot glass, then applied to the base of a vessel to hold it during manufacture. It often leaves an irregular or ring-shaped scar on the base when removed. This is called the “pontil mark.”
Faceting
The process of grinding and polishing an object to give the surface a pattern of planes
Seam mark
A slight, narrow ridge on a glass object, which indicates that it has been made in a mould.
Frosting
A matte finish produced by exposing the object to fumes of hydrofluoric acid
Casting
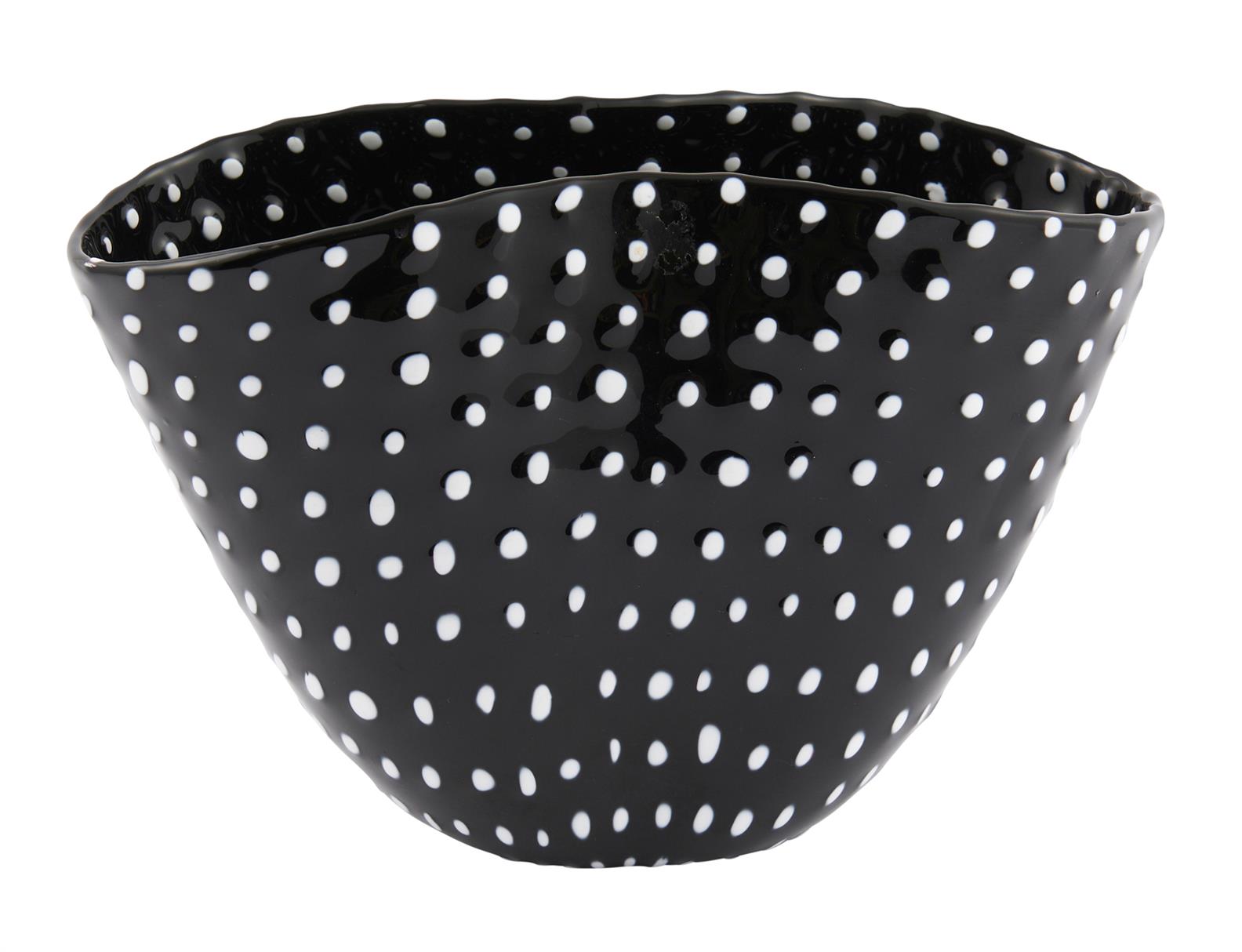
The generic name for a wide variety of techniques used to form glass in a mould including mould blowing and mould pressing.
Pâte de Verre
(French, “glass paste”) A material produced by grinding glass into a fine powder, adding a binder to create a paste, and adding a fluxing medium to facilitate melting. The paste is brushed or tamped into a mould, dried, and fused by firing. After annealing, the object is removed from the mould and finished.
Pulegoso
Glass containing numerous bubbles of all sizes, produced by adding bicarbonate of soda, gasoline, or other substances to the molten glass.
Openwork
Perforated glass objects created by either a network of trails, casting or by cutting.
Combed Decoration
Contrasting threads are rolled into the glass body after which they are combed or dragged to achieve a feathered or wavy effect.
Lost Wax Casting
As with metalworking the desired object is modelled in wax and encased in clay or plaster that is then heated. The wax melts leaving a mould for molten or powdered glass. If powdered glass is used, the mould is heated again in order to fuse the contents.
Filigrana
The generic name for blown glass made with colourless, white, and sometimes coloured canes.
Sommerso
Layering glass of contrasting colours. The two or more layers adhere and are inflated together until they have the desired form. The outermost layer, or casing, is often clear.
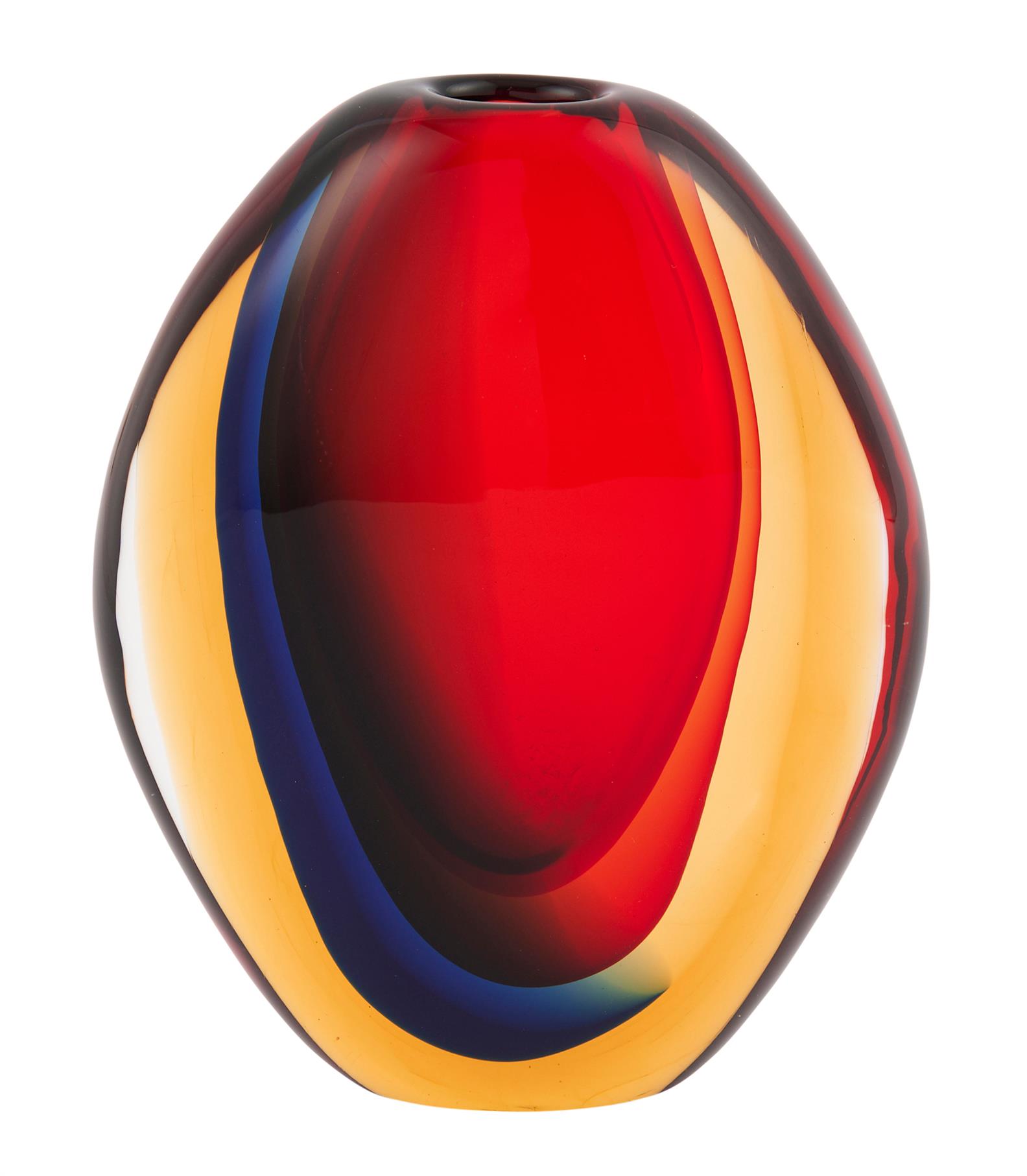
Graal
A type of decorative glass developed by Orrefors of Sweden in 1916. The design is carved, engraved, or etched on coloured glass, which is then reheated and cased in a thick layer of transparent glass and inflated.
Murrine
Cross section slices of complex canes
Iridescence
The rainbowlike effect that changes according to the angle from which it is viewed or the angle of incidence of the source of light. An effect that can be created with surface application or in the case of ancient glass occurs naturally due to the weathering process.
Slumping
The process of heating glass until it becomes soft and gradually flows under its own weight assuming the shape of the mould.
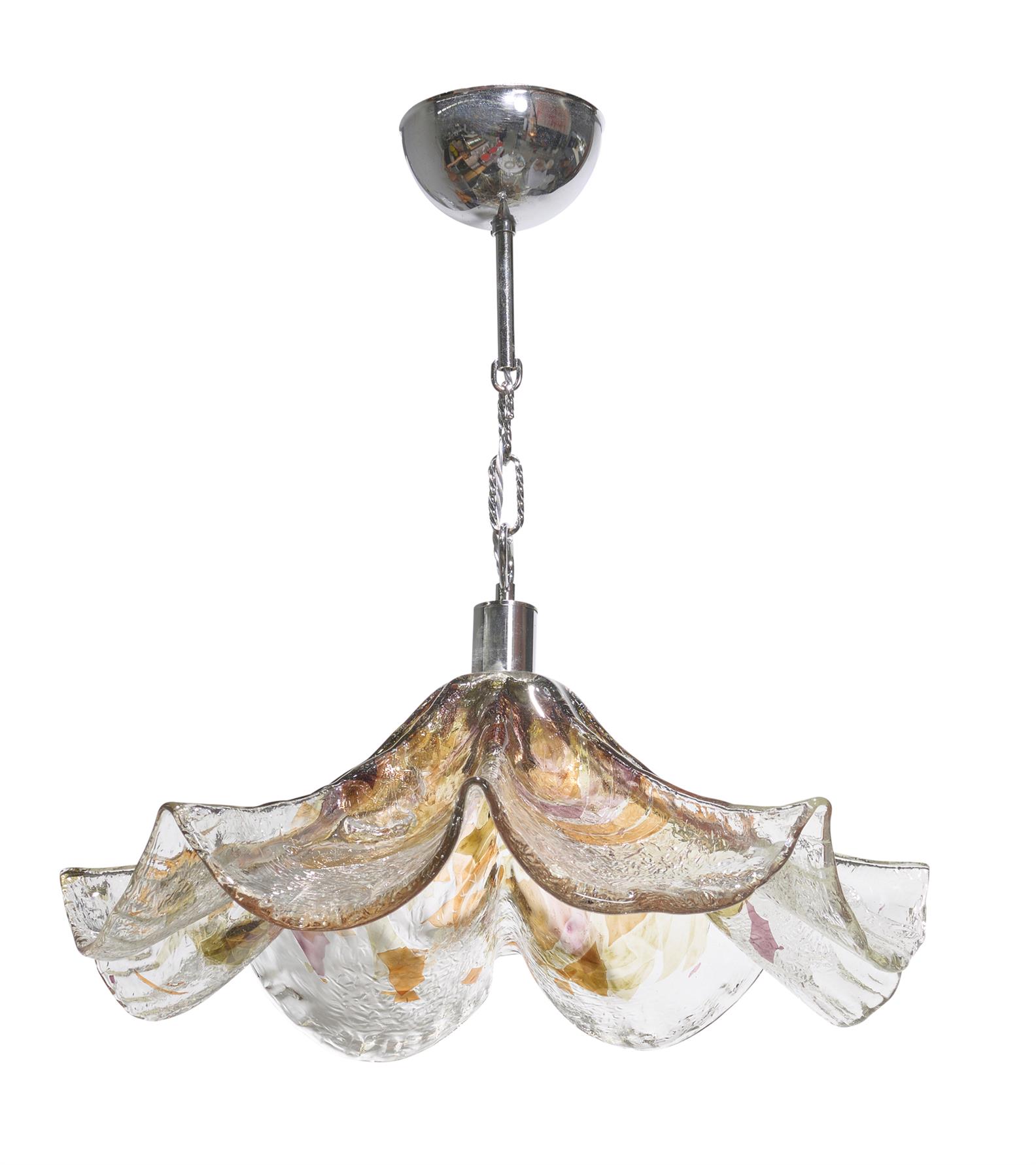
REBECCA STORMONT / Modern Design Specialist
March 2023